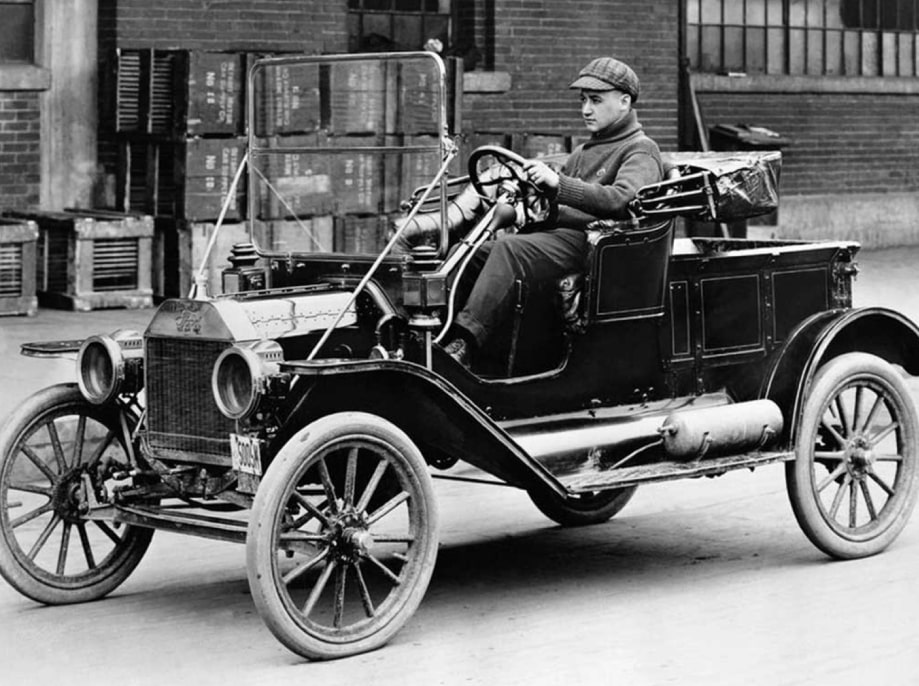
"If everyone is moving forward together, then success takes care of itself."
When Henry Ford uttered those words, do you think he knew the effect he would have on the manufacturing industry? While the quote brings to mind images of teamwork and striving towards a mutual goal, reading it knowing Ford's contributions to the manufacturing industry gives it a different meaning.
If you ask the average person who Henry Ford was, they will probably tell you he was the Ford Motor Company founder. And they would not be wrong! But if automobiles are Ford's primary legacy, then his factory manufacturing innovations are a close second.
Henry Ford was a tinkerer. As a child, he was interested in how things worked and tried to find ways to make them work better.
As a young man working in a Detroit jeweler’s shop, Ford dreamed of engineering a product that anyone could afford. His first idea was for a pocket watch that he planned to sell for 30 cents each. By his calculations, he would have to produce 2,000 watches a day to meet this low price point. Unfortunately, there just wasn't enough demand for pocket watches to sustain that level of production.
While Ford's pocket watch empire didn't succeed, he held onto his dreams of mass-production and low prices.
By the time he opened his automobile company in 1903, Ford was not new to designing cars. In 1986 he built his first car, which he christened the "Quadricycle."
Ford had a dream of making automobiles for the masses, and the Model T was the answer to that dream. Sturdy and cheap, the Model T was the 9th model Ford created and the first to achieve wide popularity. Even today, the Model T remains an icon for the still-existing Ford Motor Company.
The Model T's price was set at $850. This was cheap for an automobile, but still not cheap enough for the masses. Ford needed to find a way to cut down the price even further.
Ford consulted with Frederick Taylor, creator of scientific management, to examine the most efficient production modes. In Midwestern slaughterhouses, Ford had observed the concept of using assembly lines. He was also inspired by the conveyer belt systems used in many grain warehouses in the region. He wished to combine these ideas with Taylor's advice to create a new system for his factory.
To an onlooker, Ford's assembly line looked like a confusing contraption of chains and links. This assembly line took the process of manufacturing a Model T automobile and broke it down into 84 steps. The key to the process, however, was having interchangeable parts.
Using this method, every Model T produced on Ford's line used the exact same valves, gas tanks, tires, etc.. This allowed Model Ts to be assembled in a speedy and organized fashion. Parts were created in mass quantities and then brought directly to the workers who had been trained to work at that specific assembly station.
Ford's assembly line significantly decreased production time and greatly increased his profit margins.
Today, the assembly line is the primary mode of manufacturing in the industry. No longer used just for automobiles, food, toys, furniture, and many more items now pass down assembly lines worldwide before landing in our homes and on our tables.
While the average consumer often overlooks this fact, this 100-year-old innovation by a car manufacturer changed the way we live and work forever.