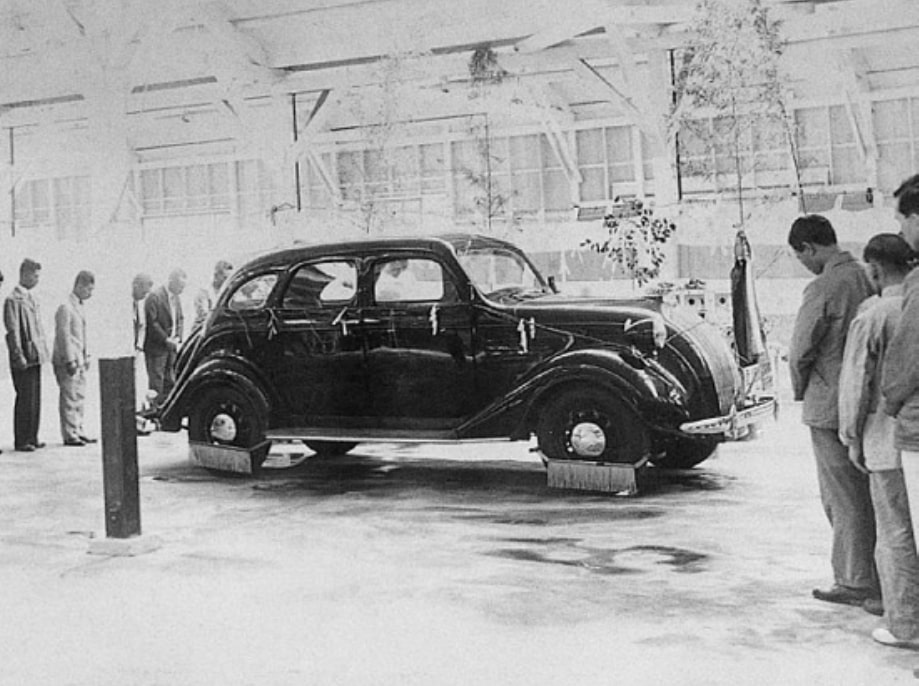
In 1933, Kiichiro Toyoda worked for Toyoda Loom Works, his family's business. While the company's focus was automatic looms used to weave cloths and tapestry, Toyoda wanted to expand the company to include an automobile division. This was considered to be a risky business at the time, but Toyoda's father believed in his youngest son's mechanical prowess and encouraged his pursuit of automobile manufacturing.
Thus, an automobile manufacturing department was newly established in Toyoda Industries Corporation. In 1936 the Model A.A. Sedan, its first production car, was released. The following year, the company's name was changed to Toyota, which has a more pleasing Japanese sound.
The company continued manufacturing automobiles and began to grow. However, when World War II broke out, the company experienced some setbacks and changes. In 1945, to help with the war effort, they stopped producing passenger cars and focused solely on trucks. Faced with wrecked facilities and a chaotic post-war economy, the company did not resume making cars until 1947.
By the 1950s, Toyota's automobile production factories were back in full operation. However, they struggled to gain a competitive hold over American cars, which were believed to be technically and economically superior. Another issue was that Toyota's level of production was far behind that of the U.S. auto industry.
That is when a young engineer named Taiichi Ohno entered the picture. Ohno began his career at Toyota working in the Spinning and Weaving division and in 1943 transferred to the Toyota Motor Company. Three years later, he was in charge of a machining workshop.
Ohno had a theory that inefficiency and wasted time were the main reasons why Toyota's production could not keep up with Detroit. He developed a list of "Seven Wastes" for manufacturing facilities to avoid. These wastes are:
1. Delay, waiting or time spent in a queue with no value being added
2. Producing more than you need
3. Over processing or undertaking non-value added activity
4. Transportation
5. Unnecessary movement or motion
6. Inventory
7. Defects in the Product.
In charge of his own machine shop and armed with this list, Ohno began implementing his theories. The machines were soon arranged in sequence of operation, established multi machine handling, and used small lot sizes. Ohno faced a lot of resistance. Nobody, from his workers to his managers, liked the new systems. For many years, it was simply referred to as the "abominable Ohno system."
Now, you might recognize it by its more commonly used name; the Toyota Production System (TPS).
Around 1970, the oil crisis hit the global automobile industry hard. Sales evaporated, as did profit. However, Japanese carmakers, especially Toyota, fared quite well.
TPS, Ohno's much-maligned system, gave Toyota the ability to quickly and efficiently produce automobiles at a lower cost. Suddenly the U.S. was much more interested in the low-priced, high-quality Japanese cars. This sudden influx led to the TPS's detailed studies, the most famous one being probably The Machine That Changed the World by Womack and Jones.
Ohno's methods helped propel the once nearly bankrupt Toyota into the third-largest automobile maker position in the world, behind General Motors and Ford.
1975, Toyota named Taiichi Ohno as its Vice President, a position he held until 1978 when he retired. "My biggest contribution was to build a production system that could respond without waste to market changes and, additionally, by its very nature, reduce costs."
Today Toyota has assembly plants and distributors in many countries. In addition to automotive products, its subsidiaries manufacture rubber and cork materials, steel, synthetic resins, automatic looms, and cotton and woolen goods. Others deal in real estate, prefabricated housing units, and the import and export of raw materials.